本篇文章內容由[中國幕墻網ALwindoor.com]編輯部整理發布:
近日,中國幕墻網ALwindoor.com獲悉:沈陽遠大鋁業工程有限公司在“超大單元幕墻”智能化、數字化生產領域取得新突破!!!
成功研發并投入應用國內首條"超大單元幕墻組裝及固化集成線",一舉解決了長期困擾行業的超規、超重等特殊幕墻單元生產難題。
行業困局
超規超重幕墻
生產“卡脖子”難題凸顯
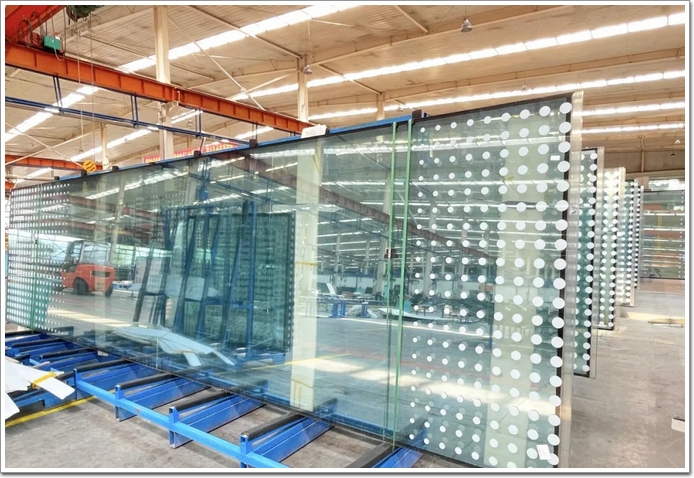
現代建筑立面造型日益復雜,施工效率與質量控制要求不斷提高,超大超重單元幕墻應時之需成為業主和設計師們的主流選擇。
這種選擇為幕墻生產制造帶來了前所未有的復雜技術挑戰。
以遠大鋁(詞條“鋁”由行業大百科提供)業現有項目中7米長、1.5噸重的幕墻單元為例,其生產過程中存在三大難點:
現有生產線設備難以適配超規尺寸
單個單元需占用多個標準工位,完全固化前無法移動,嚴重影響規模化企業的產能平衡
固化周期延長和質量控制風險等問題尤為突出
這些技術"卡脖子"難題,嚴重制約著超大單元幕墻的規;a,已成為行業亟待突破的關鍵性技術障礙。
創新破局
研發集成線
開啟生產新紀元
面對行業痛點,沈陽遠大鋁業生產技術團隊與工業工程專家組成專項攻堅組。經過多輪驗證、近百次試驗,創新性地設計出"流水施工+疊加式固化"雙核架構,實現了生產工序全周期升級:
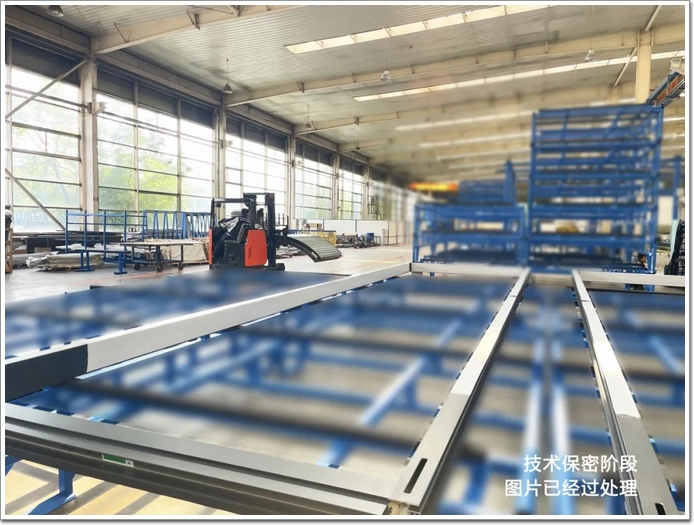
特殊設計的鋼結構承載體有效避免了單元起拱問題。運用結構力學原理,針對單元不同位置的受力差異,對每個受力點進行精準計算與特殊設計,實現不同部位的重量均勻分布,確保單元在產線作業過程中始終保持平穩。
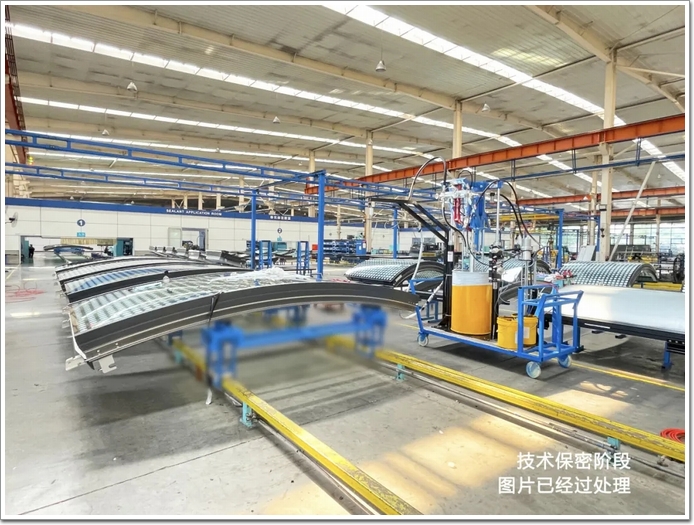
一體化工裝設計,既滿足流水線作業需求,又可作為固化架使用,實現"一裝多用"。
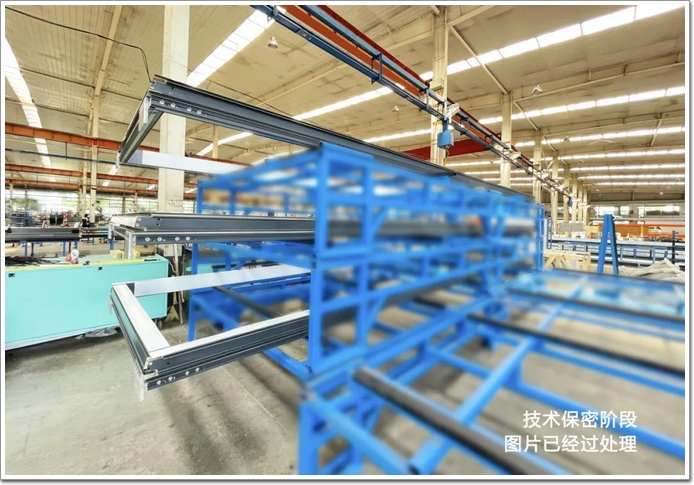
獨創的疊加式結構,實現空間集約化生產,既可單獨使用,又能層層堆疊,使空間利用率實現翻倍增長。
"這套系統就像為超大單元配備了'智能運輸骨骼',"工藝負責人解釋道,"不僅確保了生產全程的結構穩定性(詞條“穩定性”由行業大百科提供),還能實現從產線到固化間的精準轉運,在保障品質的同時大幅提升作業效率。"
成效耀局
集成線應用
帶來能效大飛躍
在實際工程應用中,該集成線表現出突出的性能優勢,為遠大鋁業超級工廠的能效提升注入強大動力。
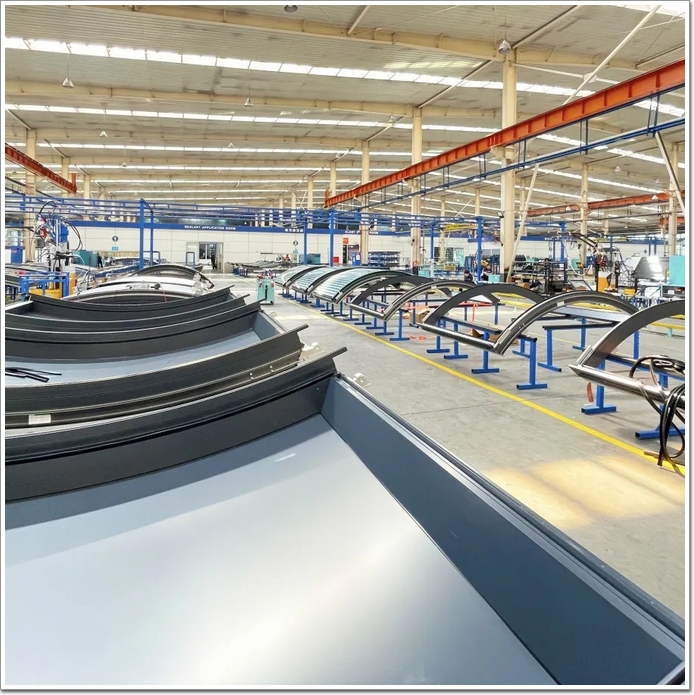
生產效率實現翻倍增長
單元生產周期較傳統模式縮短50%,大幅提高了交付能力。

空間利用大幅提升
單元固化占地面積節省67%,固化環節空間利用率提升至傳統模式的三倍,使車間布局更加科學合理。
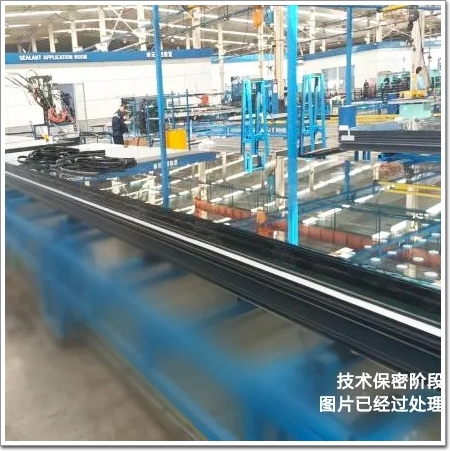
固化質量顯著提升
新系統精準控制固化環境,有效保障了單元固化所需的溫度及濕度,產品質量穩定性獲得突破性提升,為工程品質提供了可靠保障。
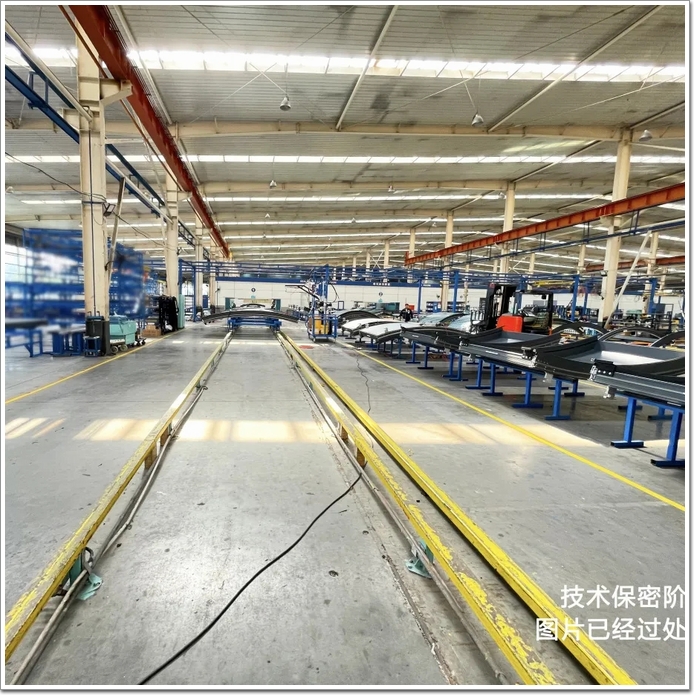
車間產能配置節省50%
新系統上線后,僅需1條生產線即可滿足原定發貨周期的產能需求,為企業節省了大量運營成本。
這一系列突破性成果,不僅解決了生產系統內多項目并行的產能平衡難題,更為整個幕墻制造行業在超大型單元生產方面提供了可借鑒的“范本”。
做為中國幕墻領域的TOP品牌、行業領軍企業的遠大,未來必將持續深化技術創新,推動幕墻制造工藝向更高效、更智能的方向邁進,為更多地標性建筑的門窗(詞條“門窗”由行業大百科提供)幕墻設計與施工提供強“大”的技術支撐。